Reacting flows
We model the complex system dynamics at the intersection of combustion, fluid mechanics, and acoustics by a systemic approach. Through the identification of three-way coupled interactions between the three subsystems (acoustics, combustion and turbulent fluid dynamics), the combustion system is modelled as a whole. Mathematical methods and high-fidelity simulations are employed to develop reduced-order models and predictive tools to simulate the flow physics. These methods are embedded into gradient-based optimization routines to help design cleaner, safer and quieter aeronautical gas turbines.
|
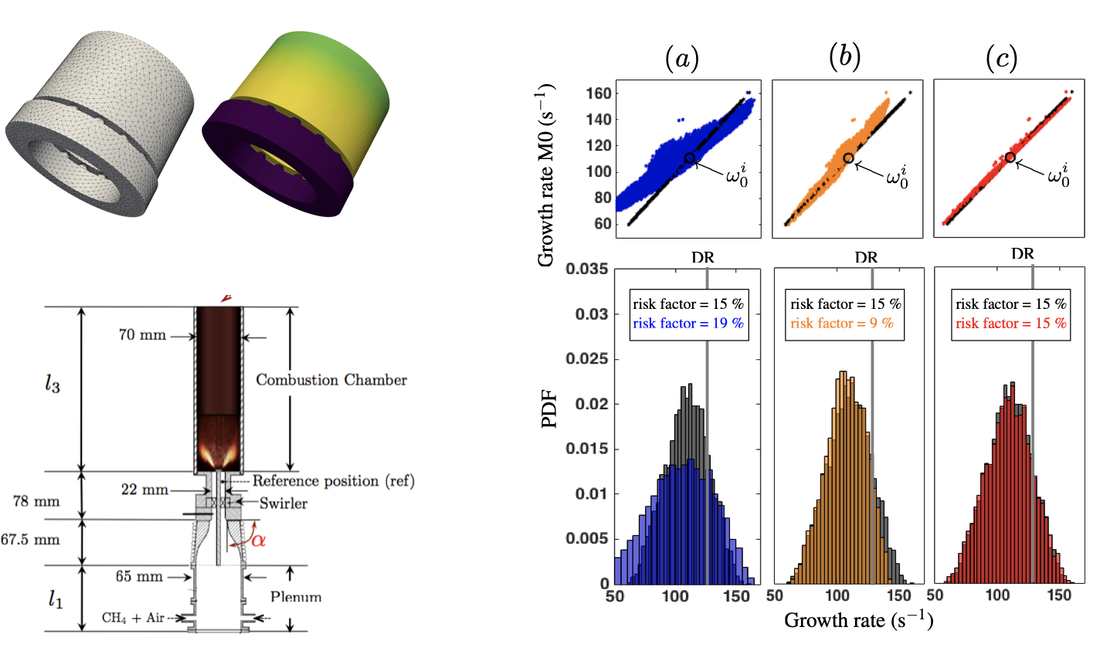
Uncertainty quantification of thermoacoustic instabilities (Stability analysis of thermo-acoustic nonlinear eigenproblems in annular combustors. Part II. Uncertainty quantification
Magri, L., Bauerheim F., Nicoud, F. & Juniper, M. P.
Journal of Computational Physics (2016), vol 325, pp. 411-421.) Applications to annular combustors (image from Effects of asymmetry on thermoacoustic modes in annular combustors: a higher-order perturbation study
Mensah, G., Magri, L., Orchini, A. & Moeck, J.
Journal of Engineering for Gas Turbines and Power, doi: 10.1115/1.4041007.) and longitudinal combustors (Uncertainty quantification of growth rates of thermoacoustic instability by an adjoint Helmholtz solver
Silva, C., Magri, L., Runte, T. & Polifke, W.
Journal of Engineering for Gas Turbines and Power (2016), vol 139(1), pp. 011901. )
Projections indicate that combustion-based energy conversion systems will continue to be a predominant approach for the majority of our energy usage for other decades. According to the International Civil Organization, global air transportation is anticipated to double over the next couple of decades, which calls for novel methods to cut back on up to 80% in oxides of nitrogen (NOx) and up to 50% in noise by 2020, as set by the Advisory Council for Aerospace Research.
Cleaner aeronautical gas turbines are designed to burn in a lean regime to reduce NOx emissions. Lean flames, especially premixed and stratified flames, burn very unsteadily because they are sensitive to the turbulent environment of the combustion chamber. Although such an environment is complex, three main physical subsystems can be identified: the acoustics, the injectors/bluff body fluid dynamics and the flame dynamics (combustion). These subsystems interact with each other contributing differently, but fundamentally, to (i) noise, (ii) thermoacoustic instabilities (also known as combustion instabilities), and (iii) rare and abrupt events, such as flashback, blowoff and flame bifurcations. All of these phenomena are unwanted and have to be eliminated during the design or controlled if they occur. Thermoacoustic instabilities are a persistent challenge in the design of jet and rocket engines: Velocity and pressure oscillations inside the combustion chamber interact with the flame and cause unsteady heat release. If moments of higher heat release coincide with moments of higher pressure (and lower heat release with lower pressure), acoustic oscillations arise. This can lead to large-amplitude oscillations causing structural damage in the jet or rocket engine. One of the most striking examples of the detrimental effects that wrong fluid design can have is the Saturn V, which is the rocket of Apollo 11 mission in 1969. The design of such a rocket suffered from violent and unexpected fluid oscillations that blew up some 2,000 engines, costing billions of dollars. The design of safer fluid systems has to be accurately guided by mathematical and numerical methods to minimize the number of experimental tests, the associated costs, and the time/resources invested. |